【案例】福田康明斯打造端到端全数字化智能工厂
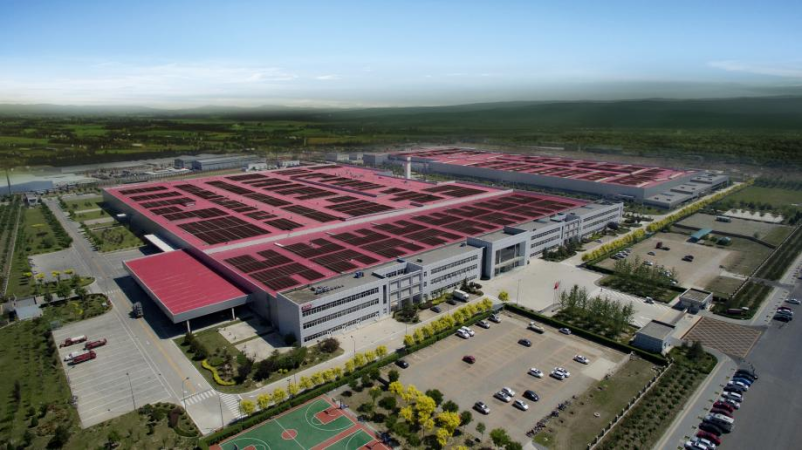
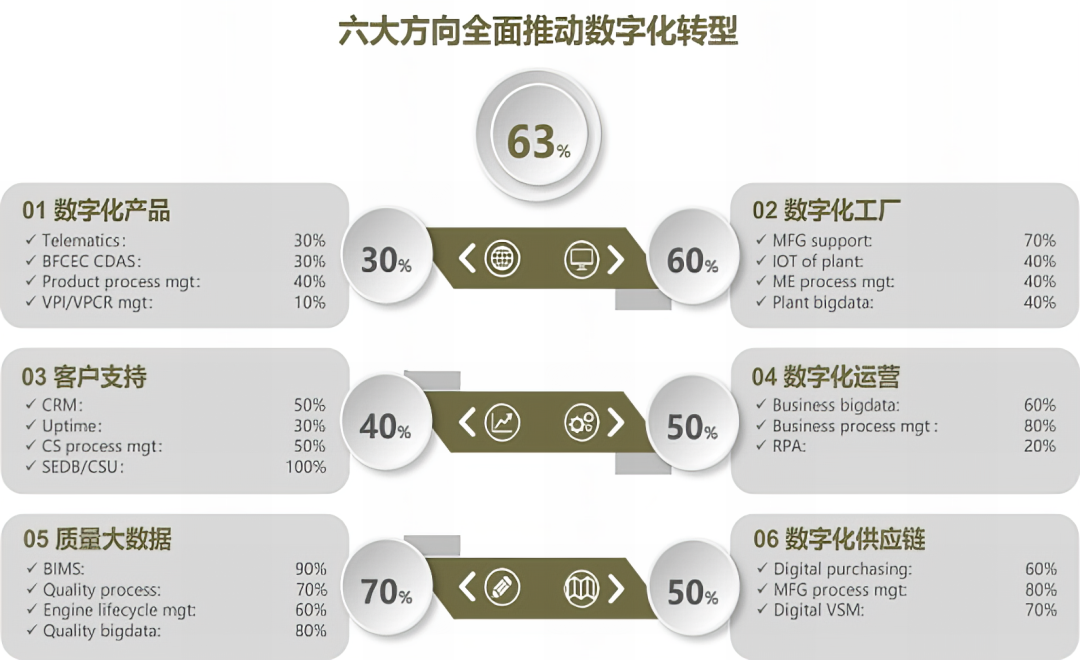
数字化转型六大方向
福田康明斯的成功,得益于其战略中的四大亮点、六大特色做法。
福田康明斯的工厂数字化平台系统,将发动机设计、制造和售后等环节数据互联互通,保证问题的可追溯性和解决的时效性。该数字化平台系统包括数据层、业务层和服务平台层,围绕产品设计、零部件管理、生产制造和售后响应等全价值流业务需求,开展工厂数据层建设;基于IOT、AI、机理模型等搭建业务层边缘计算系统,支撑实时业务需求和管理;服务平台层支撑工业APP运行的业务模型,开展AI+机理的数据分析,实现工厂的闭环管控。平台架构如下所示。
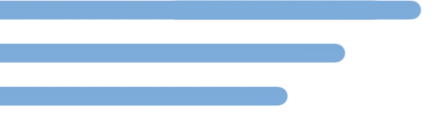
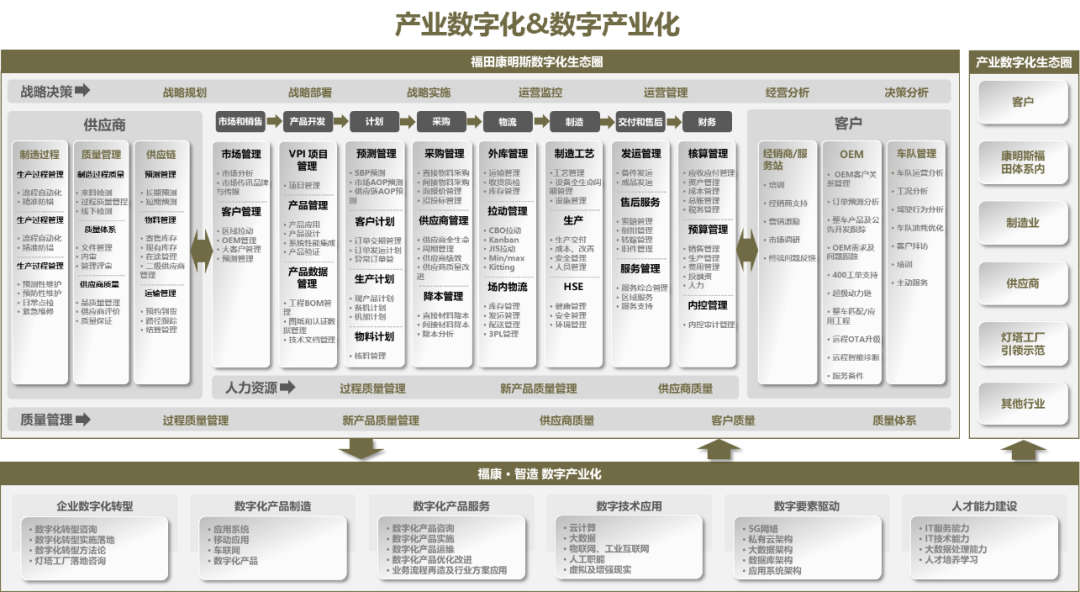
福田康明斯工厂数字化平台架构

福田康明斯配置了大量的高精度CNC、专机等设备,实现了关键零部件关键尺寸管控,采集包括功率、电流、振动等机床运行状态基础参数,并通过大数据分析,建立机床运行状态与机床加工零件质量的关联数学模型,利用“机理+AI建模”技术实现加工状态的预测,提前识别异常点。通过数据建模为设备预测性维护、刀具寿命分析等提供基础,支持建立产品健康档案、质量追溯分析等。
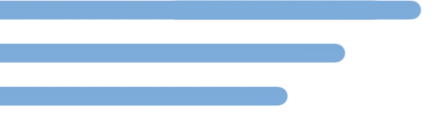
系统与机床的连接示意图
福田康明斯运用3D视觉、协作机器人、智能相机和高精度拧紧、压装和试漏等先进制造技术,建立了柔性智能装配产线,提升工厂自动化率、降本增效,保证生产过程稳定受控、提升产品质量。如识别先进制造技术在拧紧、涂胶、打磨、清洁、防错、装配、喷涂、分拣、物流等多个工艺场景下的应用,并搭建针对厂内业务需求的测试系统,开展先进制造技术应用标准化工作。
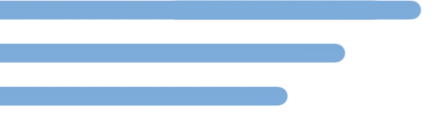
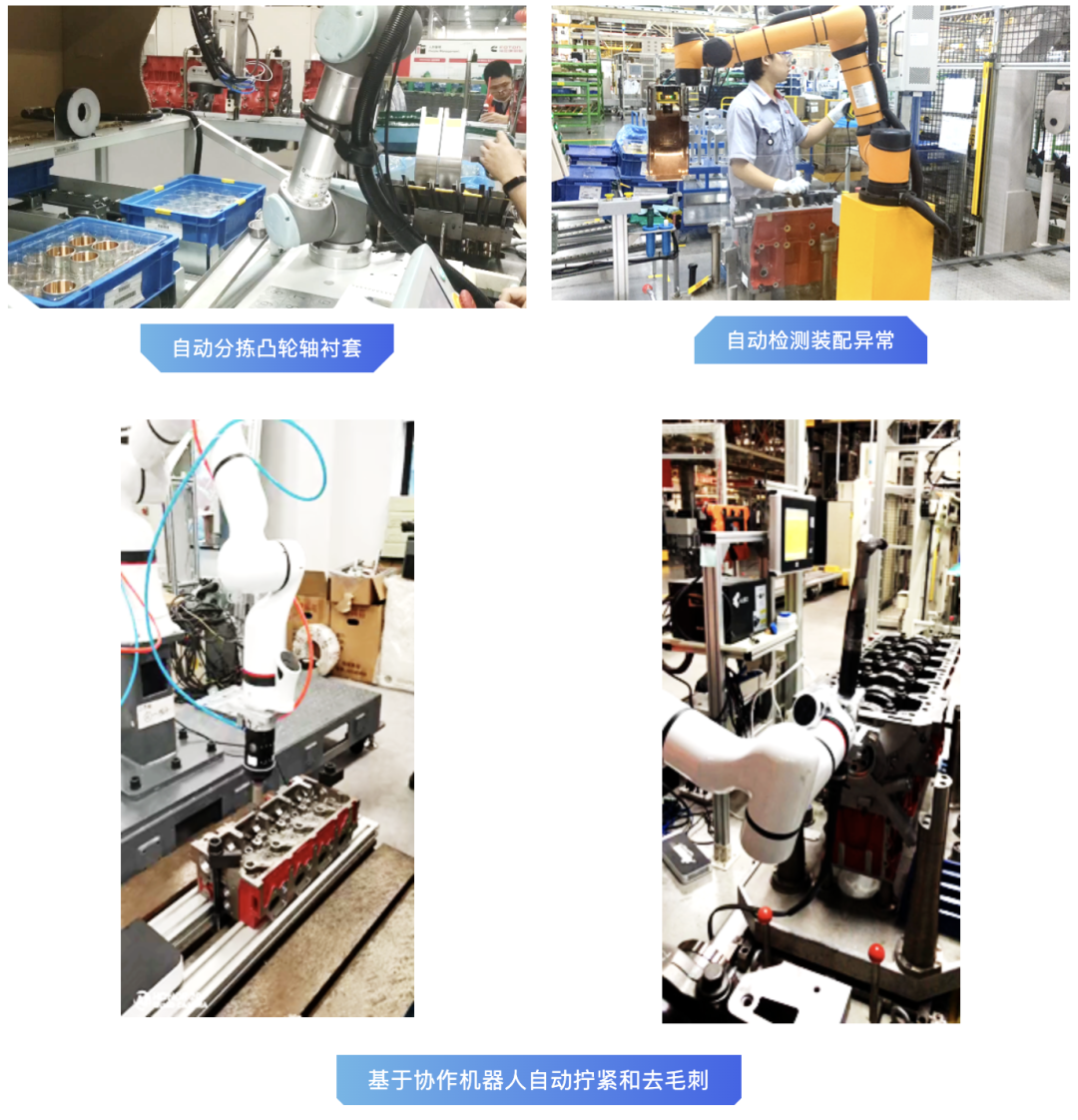

基于设备健康度管理,福田康明斯构建了设备故障预测与健康管理系统(PHM),进行设备失效模式判断、预测性维护及运行参数调优,实现设备的趋势分析、设备故障的预警管理和设备维修备件管理等。如设备物联数据全量采集后,上传工业互联平台,采用故障机理+AI分析模型、信号处理和解析、深度学习等技术,搭建设备异常检测模型和设备趋势判定模型,指导备件订购和生产维修工作,保证设备综合效率。同时福田康明斯工业APP平台搭建健康管理系统,基于多源设备历史数据,分析设备运行状态和潜在风险,实现设备全生命周期管理。
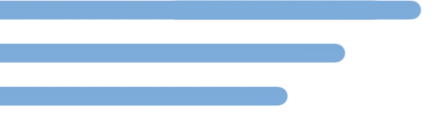
01完善、健全的基础设施——建立完备的基础架构布局,为网络化、信息化、数字化和网联化提供全方位服务和保障。
02多功能互联网络生态圈——建立了百余个信息化系统和数字化工具,建立了移动办公、知识培训、企业文化、服务支持等移动服务工具,实现了业务全覆盖。
03可拓展的工业互联网平台——打造工业互联网平台——福田康明斯数字化平台,选用开源灵活框架,支持无限扩展。
04敏捷工作模式——在应用新技术时采用了敏捷工作模式,帮助工厂在短时间内验证概念,从试点阶段进入到扩展阶段。
05深度商业智能——打造了完整的大数据技术生态,可以满足工业互联网的海量设备接入、数据采集与智能分析。商业智能渗透到生产运营每一个环节,为管理层和具体业务参与者提供决策依据。
06打通端到端价值链——实现了从供应商到客户的全流程创新,并实现从设计、订单、生产、物流、质量等全价值链可视化。