比亚迪汽车最近很火,汽车销量连续暴涨,九月份销售达到创纪录的201259辆,预计今年的销量将超过180万辆,实现汽车历史上从未有过的大跨越。现在几乎天天都能看到比亚迪的大新闻,人气冲天,销售旺盛,在手订单饱满,交车需要提前几个月排队,不管是轿车还是SUV,款款都吸睛无数,掀起了比亚迪旋风,去年才露尖尖角,今年就红遍大江南北,是什么原因引起的呢?
本文由「智造汽车」胡昌华原创,数字化企业经授权发布。胡昌华,曾任东风公司技术中心架构开发中心总师,比亚迪第十一事业部技术中心总装工艺专家。
世上没有无缘无故的爱,更没有毫无厘头的爆发户。通过认真的观察,仔细分析,静静的思考,总的来看比亚迪汽车成绩斐然完全是技术能力厚积薄发的结果,是超级产品力赋能的体现,从而开创了比亚迪汽车新时代,下面总结的八大核心技术就是其典型代表。
比亚迪发明的刀片电池是指电芯像刀片一样扁平且长条,是基于方形铝壳来做的一种长电芯电池方案,正极材料采用磷酸铁锂,负极材料为人造石墨。虽然没有在材料上进行重大的创新,但刀片电池在结构和工程技术上是全球首创,在比亚迪原有的电芯的尺寸基础上,减薄电芯的厚度,增大电芯的长度,将电芯进行扁长化及减薄设计。
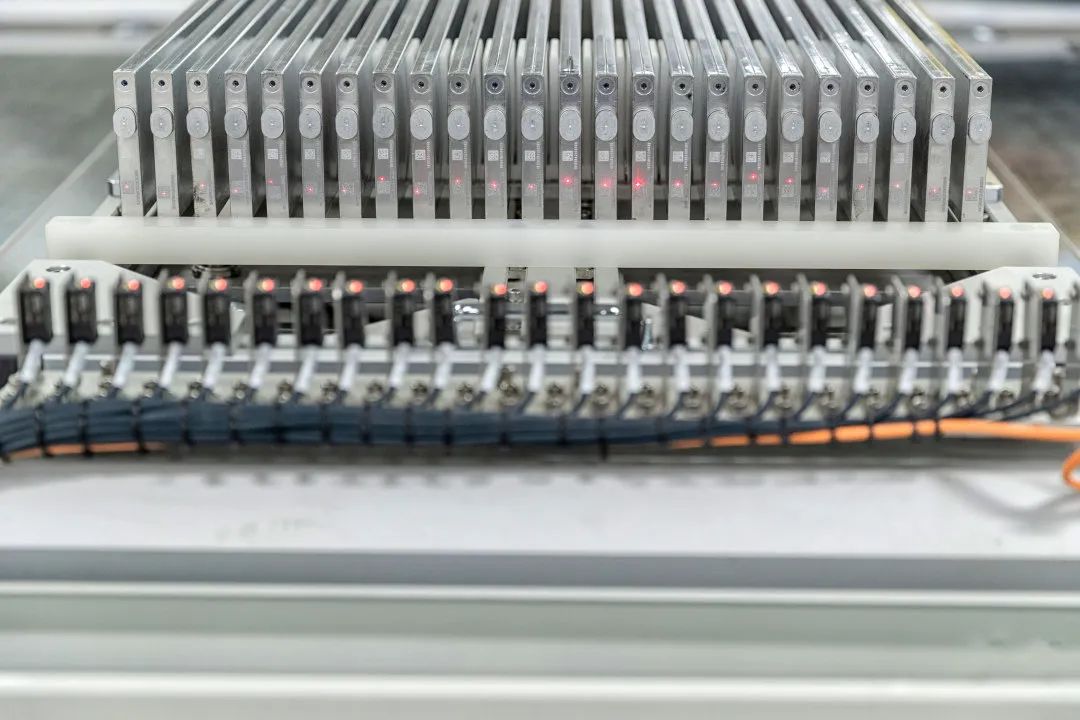
同时刀片电池包将电池阵列作为骨架,通过高性能胶黏剂将上盖、底板与电池阵列粘合成一个整体,实现超高集成效率,超高强度和刚度。与传统的技术电池系统相比,采用刀片电池的电池系统零部件数量减少40%以上,比能量密度虽然只提升了9%,但VCTP体积能量密度可增加50%以上,成本可下降30%以上。
目前刀片电池有单串刀片电池、多车刀片电池和多串方块电池三大类,灵活性高,多种长度厚度可供选择,同时刀片电池本身的结构就可以充当横梁和纵梁的结构,同时在电池包的上层和下层增加蜂窝铝板的机构,大大的提升了电池包的结构强度。比如比亚迪DM-i系统搭载的专用功率型刀片电池,单节电压超过20V,单节电量最大1.53度,传统电池包有近100节电芯,而内串刀片电池的整个电池包,只有十几节电芯,大大较少了电池间的连接,零部件个数减少35%。比亚迪刀片电池在安全、寿命、低温、充电、功率及能量等六大关键性能指标方面都处于领先位置,为比亚迪电动车赢得了极好的声誉。
比亚迪持续不断地研究DM混动技术,2008年,成功研发出第一代DM技术,采用双电机串并联结构;2013年,比亚迪推出第二代DM技术,采用水冷电机与双离合变速器相集成(P3),匹配发动机组成混合动力总成,并在后轴增加驱动电机(P4),形成三擎四驱系统,实现了百公里加速5秒以内的惊人成绩;2018年,比亚迪在第二代DM技术的基础上,增加开发了PSG辅助电机(P0),使双模车的动力性、经济性和平顺性全面提升,称之为第三代DM技术;2021年,比亚迪重磅推出第四代混动技术DM-i,实现了插电式混动领域上新的突破。亏电油耗百公里3.8升、油电综合续航里程超1200公里、百公里加速7秒级别,搭载在秦PLUS、宋PLUS、唐、汉等车型上,成为市场主流混动技术,带领车型大卖。
比亚迪的DM-i超级混动技术的核心组件包括:骁云插混专用发动机(其中有两个不同的版本——1.5L发动机主要用于秦PLUS、宋PLUS;而1.5T涡轮增压发动机则用于更大型的唐DM-i车型)、EHS双电机、专用刀片电池,加上一系列的整车控制系统、发动机控制系统、电机控制系统、电池管理系统,共同构成超级混动系统。
EHS电混系统是DM-i超级混动技术的核心,它集成了双电控,双电机和离合模块。两台电动机一台负责发电,另一台负责驱动和能量回收,采用了扁线绕组技术的两台电机转速可达16000rpm,拥有非常宽泛的经济区间,最高热效率达到97.5%,相同功率下电机的体积更小,更节能。
EHS电混系统采用串并联结构,由双电机、双电控、直驱离合器、电机油冷系统、单档减速器组成,可实现以下几种工作模式:
(1)EV纯电驱动模式:起步或中低速时,发动机不启动,由驱动电机单独驱动车辆纯电行驶,在市区开车就相当于是一辆纯电动汽车;
(2)HEV串联模式:中高速行驶时,发动机工作在最佳经济区间,带动发电机进行发电,电能驱动驱动电机,维持电量平衡。当发电机供电不足时由电池向驱动电机补充电能,当发电机供电充足时,额外电能向电池充电。
(3)HEV并联模式:高速行驶或大功率输出时,发动机与电机共同驱动车辆。
(4)发动机驱动模式:高速巡航时,离合器结合,发动机工作在最佳经济区间。
DM-i超级混动系统以电为主、以油为辅,当DM-i车型电量充足时,就相当于一台纯电动车,电机的动力供应足够在各种路况下行驶,而当电量不足时,DM-i车型就会根据系统工况,自主判断用电还是用油,亦或是油电协同,既能享受电动汽车的驾趣,又能长途行驶里程无忧,满足了大多数用户的需求。
比亚迪研发的八合一高效电驱总成,集成了驱动电机、减速器、驱动电机控制器、高低压直流转换器(DCDC)、双向车载充电器(OBC)、高压配电箱(PDU)、电池管理器(BMS)、整车控制器(VCU)八大模块,其整体性能较上一代功率密度提升20%,整机重量和体积分别降低15%、20%,系统综合效率达到89%,其最大功率270kw,具备前驱、后驱、双电机四驱三种驱动形式,满足A0级到C/D级车型动力搭载需求。
◉ 驱动电机:采用发卡扁线永磁同步电机、超薄硅钢片,电机功率提升40%,最高效率97.5%。且能够平台化覆盖70-270kw。
◉ 减速机械机构:应用低摩擦轴承,导油式结构,提升润滑效果且降低搅油损失,齿轮精细设计降低齿轮滑移损耗,同时首次应用低粘度油品,传动最高效率97.6%。
◉ 电机控制器:VCU、BMS、MCU(含DCDC、OBC、PDU配电升压类)深度集成,相对独立式,电控系统相应时间缩短90%。同时节省大量高压线束,模块体积缩小40%。
比亚迪八合一电驱总成集成度高,系统软硬深度融合,是全球截止目前唯一一家能够开发且量产八合一电驱总成的车企,核心在于其对功率模块、芯片的产业链掌控。
所谓CTB技术(cell to body),即电池与车身一体化技术,同步设计电池包和车身底板,将车身底板+集成电池上盖+粘接剂+电芯+粘接剂+托盘组成一个整体,也就是说将将电池包与底板融于一体,电池包上壳体替代了中地板的一部分结构,让电池包直接成为车身结构的一部分,电池包上盖与门槛及前后横梁形成的平整密封面通过密封胶条密封乘员舱,底部通过安装点与车身组装,这样动力电池包既是能力体,又是结构体,在减低车身自重的同时,又加强车辆的整体强度。
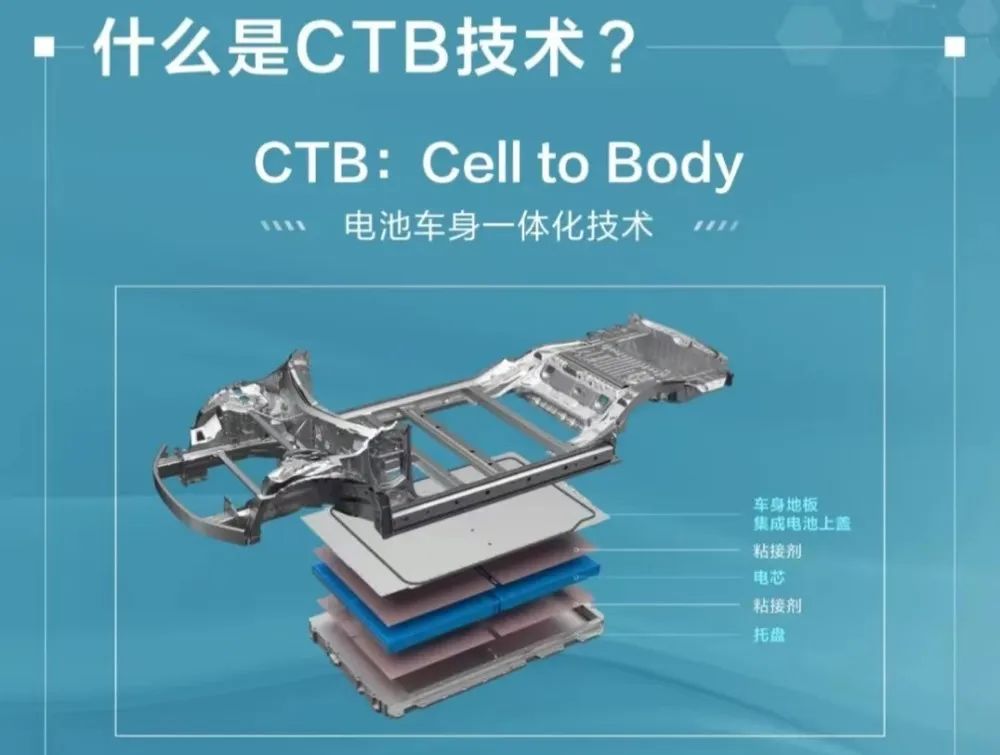
CTB技术融合了电池包壳体、车身结构和装配工艺设计的技术,是对新能源车身设计及总装工艺技术的一次颠覆性变革,CTB技术首发车型为海豹,该车型一上市即成爆款。
近两年来,比亚迪汽车整体造型及内外饰的演变明显改变了人们对国产车的审美印象,高端、大气、上档次,完全媲美德、美、日品牌的豪华车,
不管是王朝系的元、秦、宋、唐、汉,还是新推出海洋系列的驱逐舰、海鸥、海豚、海豹、海狮,其外观造型都非常适合中国人的主流审美意识而又不失其引领潮流的现代感。
这一些的变化是继2016年奥迪前设计总监沃尔夫冈·艾格正式加盟比亚迪成为比亚迪的设计总监、前法拉利外饰设计总监欢马·洛佩慈和奔驰前内饰总监米歇尔·帕加内蒂于正式加盟比亚迪而起到了大师级的引领作用,提升了比亚迪汽车的整体造型技术水平和审美高度,极大的促进了汽车的销量。
比亚迪汽车工厂实现了超柔性生产制造,除生产线具备多平台多车型混流生产的软硬件条件外,整个物流系统也有别于传统车企的模式,比亚迪每个生产基地的商品车停车场只能最多存放三天产量的整车,为了节省面积,有些基地还建成了立体存车库。比亚迪的理念是将传统车企的整车库存模式转变为零部件的中间库存模式,工厂严格按订单组织生产,全力以赴保交付,形成了具有比亚迪特色的超柔性生产制造体系。
举个立体车身库的例子,比亚迪的超柔性生产制造系统关键技术之一就是建立高度自动化和智能化的焊装白车身立体库和涂装彩色车身立体库。彩色车身库整个仓库位于涂装和总装车间之间,一方面它承担着涂装车间生产的彩车身的存储缓冲作用,另一方面它又能根据总装车间订单顺序变化对彩车身进行实时排序出库,精确排产后的车身到总装上线点有满足2小时生产的车身数量,便于总装排序上线零件的准备及拉动总装所需零部件的准备。彩色车身立体库实现了车身从出涂装—分配库位-入立体库--出库-排序-进总装全流程的智能化、自动化运行,实现了安全、稳定、高效、精准的车身仓储管理,同时车身实现了同一颜色车身批量涂装,降低了频繁换颜色的油漆损耗,总装按班生产计划及经济批量排序生产,同时也降低了管理成本和物流成本。
某基地彩车身立体库高17.2米,包含仓储区和输送区。仓储区包含7个巷道,规划了7台双立柱堆垛机以及917个货位、7个维修货位。输送区共设计四层输送线,一层:对总装二线出库;二层:对总装一线出库;三层:涂装一线入库;四层:涂装二线入库。整套系统高效快速,生产节拍可达120JPH,出入库自动化输送线与生产线柔性连接,实现了立体库与车间输送线的智能化转接。
比亚迪彩车身立体库采用定制化的WMS系统,并与比亚迪的终端系统MES系统无缝对接,实现对整个物流系统进行全流程的管控。WMS将库存信息上传到MES,然后MES将库存信息与生产计划做匹配;用户直接通过MES将计划内的库存车身出库任务下发到WMS,WMS按照顺序安排出库。
为了提升插电混动车型和纯电车型的电动续航里程,电池包的尺寸设计也越来越大,越来越宽,比亚迪的工程师们开发了以满足超宽电池包合装技术为特色的一系列混动/电动汽车制造的新工艺新技术,满足了不同尺寸大小的混动车/电动车的混流生产及质量保证要求,特别是在总装底盘合装后设计了一条电池包合装线,采用车身载具托车轮的方式,完全释放了装配工艺上对电池包大小的限制,为比亚迪汽车大批量高节拍生产新能源汽车奠定了技术基础。
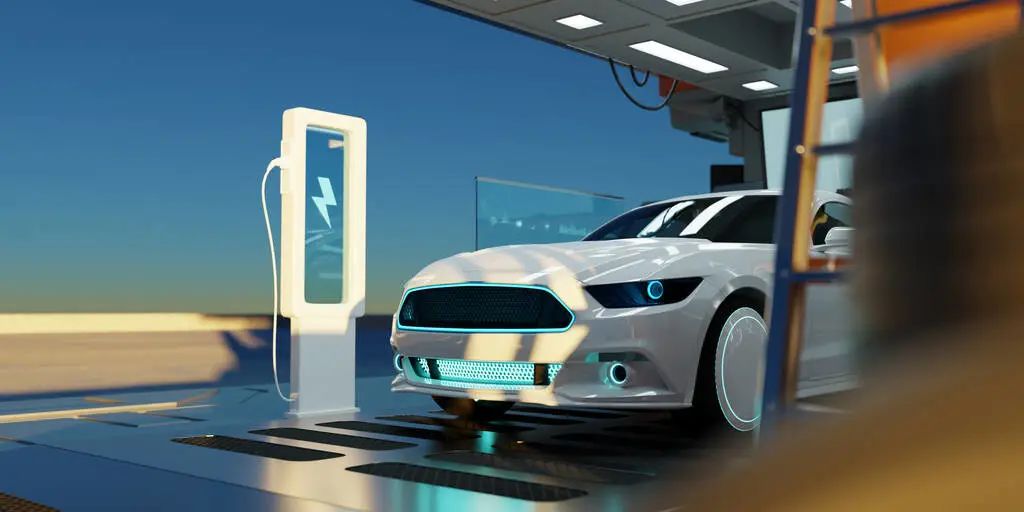
超宽大电池包合装技术是比亚迪先进的新能源汽车制造工艺技术之一,这些核心制造技术的掌握及应用为比亚迪大批量低成本、高质量制造新能源汽车奠定了基础。
比亚迪深度布局、垂直整合新能源汽车产业链,从上游原材料到中游零部件再到下游整车,形成完整闭环,产业链协同效应显著。成立弗迪电池、弗迪动力、弗迪视觉、弗迪科技、弗迪模具(弗迪精工)五家弗迪系子公司,进一步加快新能源核心零部件的外供业务,所谓的“垂直模式”是一种纵向一体化模式,即将供应链一个一个环节进行分解,形成垂直一体化,纳入自己体系当中。换句话说就是“能自己做的都由自己来做。”
除了汽车轮胎和玻璃,比亚迪具备了几乎所有核心零部件的自主研发生产能力。得益于这一模式的顺利实施,比亚迪通过对于上游原材料成本的控制,最大限度的降低了生产成本并极大的提高了生产效率,这使得比亚迪拥有了低成本的竞争优势。在进入汽车行业之后,比亚迪就开始对整个汽车产业链进行布局,上至电池金属原材料,下至汽车模具、IGBT……比亚迪供应链体系,简单来说,就是垂直整合,能自己造的汽车元件就自己造。车身上所有钣金件都是自己冲压的,模具是自己造的,车身上的焊点都是自己焊的,夹具是自己造的。不仅自己造动力总成零件,而且自己造底盘零件,不仅造机械件还造自己造电器元气件,比如线束、安全气囊、大灯、控制器等。
比亚迪在规划设建整车生产基地时不仅规划建设整车厂生产所需的完整的冲、焊、涂、总工厂,而且同步规划建设自己的零部件工厂,主要建设了塑料件工厂、线束工厂、车灯工厂、底盘件工厂、电动总成工厂、电机工厂、精工中心、齿轮工厂、电控工厂、电源工厂、制动器工厂等新能源汽车核心零部件生产工厂。
另外比亚迪2020年正式成立比亚迪半导体事业部,负责研发生产包括车规芯片在内的各类集成芯片,把新能源核心芯片业务也牢牢掌握在自己的手中。
比亚迪汽车供应链上的企业都是独立核算的,有严格的考核指标,在满足自身高速度发展的同时,还承担了对外合作和销售任务,动力电池、安全气囊、热管理系统等重要零部件都对外销售,参与市场竞争。
比亚迪的零部件深度垂直整合技术,能让全产业链齐心协力,上下依令而行,为比亚迪新车型开发赢得了时间和成本优势,在这个快鱼吃慢鱼的时代,想不成王都难。
总之,比亚迪汽车公司在以“技术为王,创新为本”的发展理念指导下,长期坚持在主业产品研发上投入大量的资金和人力,取得了丰硕的技术创新成果,本文总结的八大核心技术只是这些成果中最重要的一部分,也是改变比亚迪汽车形象、开创比亚迪汽车新时代的核心技术成果。
创新和技术研发焕发了比亚迪汽车的勃勃生机,事实再次证明并将继续证明,中国的汽车工业只有实实在在地创新,踏踏实实地研究,掌握核心技术,才能在新能源汽车浪潮中阔步前行,闯出一番新天地,改变原有的汽车工业格局,实现超越式发展。