引自:《智能装配工艺与装备》(作者:张开富、程晖、骆彬)
在航空航天产品生产中,生产工艺对产品生产效率和生产质量产生了重要影响,采用智能制造的方式不但能够提高装配生产效率,同时还能满足装配生产需要,解决装配生产问题。基于航空航天装配生产实际,智能制造的应用对航空航天装配生产具有重要影响。智能制造技术集合了人工智能、柔性制造、虚拟制造、系统控制、网络集成、信息处理等学科和技术,由智能装备、智能控制和智能信息共同组成的人机一体化制造系统,能够实现制造过程自动化、智能化、精益化、绿色化,是传统产业转型升级发展的重要途径,因此,智能制造已成为我国航空航天制造业新一轮产业技术变革的主要方向之一。
飞机智能装配应用系统是实现飞机智能装配的重要支撑,按照飞机“组件—部件—总装”的装配流程,相关的装配系统可以分为3大类:飞机组件智能装配单元,飞机部件智能装配系统,飞机总装智能装配生产线。目前,智能传感器、射频识别技术、智能机器人、信息智能处理等一些装配基本单元和技术已在飞机装配中得到初步应用。然而,飞机装配的完全智能化还需要进行更多的系统顶层研究,尤其是对各个层次的飞机智能装配应用系统集成研究。
与传统的航空生产车间不同,飞机智能装配单元中大量的智能设备与人组成了一个协同的智能装配环境。传感器安装在网络可用的装配区域,记录关键制造数据;RFID校验工具精度、机械状态以及工人资质等;感知代理能够完成动态、调节性的过程监控,在正确的时间,将正确的信息提供正确的人;激光发射器能够显示工程和缺陷定义,探测物体3D空间的位置;室内GPS能够提供实时的位置数据给智能手持工具以发现缺陷;智能手持工具借助网络获取位置信息和加工需求,在加工过程中,智能手持工具又将实际位置和加工参数传递给网络,系统通过网络校验,确认操作的正确性。
「 2. 飞机部件智能装配系统 」
将工业机器人和特种机器人(爬行、柔性导轨以及蛇形机器人)应用于飞机装配系统,将使飞机装配具备数字化、自动化、柔性化和智能化的特点。多家智能设备公司均开发了柔性导轨制孔系统,大量应用于波音、空客等飞机的装配作业。图1为波音公司开发的模块化柔性导轨制孔系统,柔性化且满足高质量制孔要求等特点。图2为一种爬行机器人自动制孔系统,工作时,机器人通过真空吸盘将自身固定在飞机产品上,在视觉系统的帮助下完成位置坐标的自适应调整,在其工作空间内完成制孔作业。
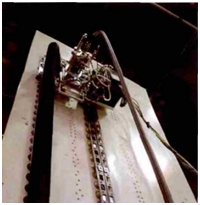
图1 模块化柔性导轨制孔系统
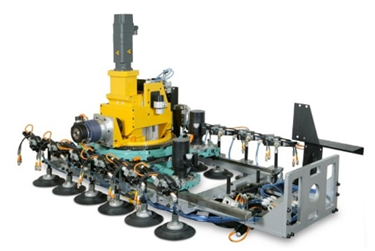
图2 爬行机器人自动制孔系统
其他飞机部件智能装配系统还包括测量辅助机器人定位系统、多功能钻铆末端执行器、自动托架系统、力位多传感调姿定位器、调姿定位控制系统、调姿在线测量系统、调姿系统软件、AGV等。
工业机器人由于其空间定位精度不高,不能直接工业机器人由于其空间定位精度不高,不能直接量手段对工业机器人进行二次定位测量标定,才能满足飞机的高精度装配要求。工业机器人会随着其承载力、运动惯量、铆接冲击力、末端执行器重心的变化等影响其空间定位精度。因此针对工业机器人不同的作业要求,在其末端执行器上安装六自由度测量仪,或者制作专用的标定工装。通过测量机器人当前的空间位姿,与系统设定的位姿进行对比分析,计算出机器人的位姿偏差矢量信息与其补偿量,通过对机器人进行误差补偿,实现其精准定位功能。
多功能钻铆末端执行器具有照相测量、法向检测、自动制孔、自动铆接等功能,是多种智能特性的集成体,能够提高装配柔性、装配效率及减少成本。多功能钻铆末端执行器主要由照相测量单元、法向测量单元、自动制孔单元和自动铆接单元等组成。
(1)照相测量单元:控制系统通过以太网发送采集命令,同时打开光源,在光源的照射下,CCD照相机开始拍摄工件的图像,通过图像处理与分析软件分析待测工件的图像,得出待测工件的尺寸参数,计算出定位孔的坐标值,并与理论坐标相比较,判断工件定位孔的位置偏差,并且通过数据线把数据反馈给控制系统进行二次定位,保证了最终的孔位置度。
(2)法向测量单元:法向测量单元用于检验和调整钻孔和铆接时末端执行器与蒙皮表面的位置关系,保证钻铆操作时的法向精度,提高钻铆质量。
(3)自动制孔单元:自动制孔单元完成蒙皮与铝合金等夹层材料的制孔操作,其设计制造需综合考虑钻孔主轴电气参数、安装尺寸和安装方式等因素,避免与其他单元部件产生干涉。
(4)自动铆接单元:铆接单元主要完成制孔后的铆接操作,其设计和制造需考虑铆接方式对安装方式及结构的影响、铆钉输送机构的动作、铆接冲击力对末端执行器和机器人结构的影响等因素。
自动钻铆全自动托架系统的设计与制造需要基于现有自动钻铆机展开,该系统清晰体现了自动调姿对接等智能特性,同时突破了自动钻铆离线编程与仿真软件设计、系统集成控制等难点。
力位多传感调姿定位器是实现自动调姿对接特性的典型机械传动装置。力位多传感调姿调姿定位器一般为三坐标结构,分别由底座、运动组件和连接接头等组成,运动组件有X、Y、Z向驱动。定位器带有锁定机构,用于完成调姿后对壁板等零部件姿态进行锁定;并配负载传感器实时监控X、Y、Z共3个方向承受的力,并设定报警力,超过报警力及时报警。其主要特点包括:应力检测、入位检测、入位锁紧、限位保护。
调姿定位控制系统是实现自动调姿对接特性的电气控制基础。调姿定位系统功能是实现飞机零部件的调姿定位和支撑,是通过多个数控定位器联动实现的。调姿定位控制系统应具有如下特点:装配调姿定位实现全数字化控制;高精度多轴协同伺服控制,实现零部件精确姿态调整和定位;具有柔性化特点,能够在行程范围内对机身壁板等进行柔性化调整;具有多种状态检测与安全防护功能,保证产品;具有多种状态检测与安全防护功能。保证产品电气控制系统功能:单坐标轴闭环伺服控制,实现单坐标精确定位;多轴协同运动控制,实现部件精确调姿;I/O逻辑控制,实现工艺球头入位检测、锁紧;I/O逻辑控制,实现限位检测、应力检测、紧急停止等安全防护功能;工况监视,监视并记录重点部位现场工况,增强装配安全性;多种操作方式,自动、手动和方便近距离操作的手持式操作。
数字化装配测量系统的作用主要是:完成大范围的空间测量,协调对接系统和制孔系统之间的坐标关系;完成水平测量点的在线跟踪、数据采集,将测量结果实时传递到集成控制系统中,为零部件的姿态评估和调姿提供数据支撑。硬件系统主要包括了测量仪器硬件主机、数据线、控制箱、测量软件、数据分析模块、电脑服务器等。针对不同的数字化测量设备,可以采用相同的测量软件,需要开发与调姿系统、自动运输设备之间的数据接口程序,将测量模块加载到集成控制软件中。根据测量设备的特性,可以采用不同的测量环境布置和测量点设计方案,用于装配坐标系的统一、设备的安装、运动精度的标定、定位器的到位检测、产品的调姿与到位检测等。
7)调姿系统软件
调姿系统能够完成零部件上架、姿态测量、调姿路径规划和自动调姿运动控制等功能,能实现零部件姿态的自动评估和优化,能实现运动过程的模拟仿真,进行姿态正确性评估,能实现调姿过程的实时监控和可视化显示,形成调姿过程日志。系统实现与现场测量系统(iGPS和激光跟踪仪)以及数控定位器控制系统的集成,能实时采集现场测量数据,实现数据的实时计算和位置姿态的评估,并能实时监控定位器各个运动轴的位置及运动状态等。调姿定位系统处理流程主要包括:系统初始化零部件上架姿态测量、调姿路径规划、调姿运动控制、到位检测、调姿报告等部分,其中的姿态测量到位检测环节会多次重复进行,如图3、图4所示。
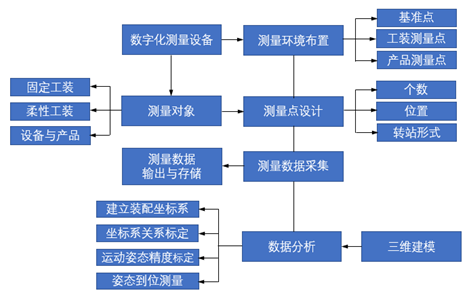
图3 调姿系统测量流程
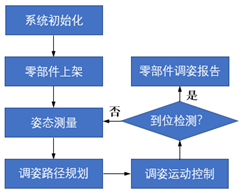
图4 调姿系统控制流程
「 3. 飞机总装智能装配生产线 」
飞机总装智能装配生产线在航空制造领域的应用是飞机数字化柔性装配技术的一个重要发展趋势。目前,国外已在飞机的总装生产中应用了移动生产线或脉动式生产线,以提高飞机的生产率和质量。
美国F35战斗机建立了完整的数字化智能装配移动生产线,实现了装配过程全自动控制、物流自动精确配送、信息智能处理等,达到了年产300架的能力。波音公司在波音777的飞机总装配中应用了移动装配生产线(图5),使得生产系统更精益且更有效。在提高生产效率和质量的同时,还能使制造飞机的人员得到更大的保障。
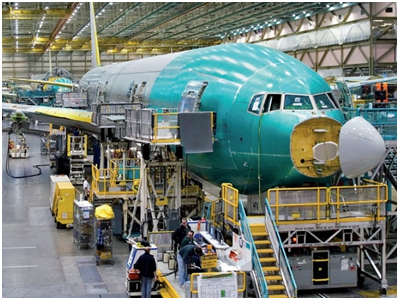
图5 波音777总装移动生产线